Jobs
Showing 1047 results
Sort by:
Process Engineer II
Position Summary:We are seeking a highly motivated Process Engineer II to support the design, implementation, optimization, and scale-up of pharmaceutical manufacturing processes. This role is critical in ensuring that production processes meet quality, safety, and regulatory requirements while achieving operational efficiency. The ideal candidate ...
Sales Representative
Sales Representative - Innovative Product SolutionsWe're looking for a driven and results-oriented Sales Representative with a strong background in sales and market knowledge. This role centers on promoting innovative product solutions through engaging, hands-on demonstrations and strategic use of samples to highlight product value. If you excel at...
Operations Manager
OPERATIONS MANAGER Overview:A leading semiconductor manufacturer is seeking a hands-on, results-driven Operations Manager to lead and optimize its plating operations. This is a critical, multi-functional leadership role focused on improving capacity, cycle times, staffing, and inventory flow in a vertically integrated production environment.Core Re...
Elevate your career
Take the first step toward your next opportunity - submit your resume and get started today.
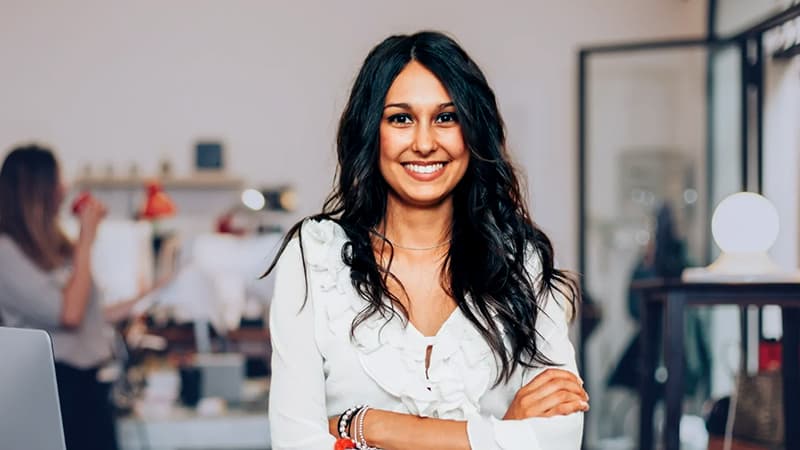
Validation Design Engineer
Position Overview:DSJ Global has partnered with a Power Electronics Manufacturer in the Greater Boston Area looking to bring in a Validation Design Engineer. This position is a key part of expanding their team and will be responsible for working closely with NPI Program Management and Manufacturing teams to drive new product development while impro...
Controls Engineer
We're looking for a skilled Controls Engineer to play a key role in supporting the Cleveland-based manufacturing site. This position is ideal for someone with strong technical expertise in automation, control systems, and industrial equipment who thrives in a hands-on, problem-solving environment.Role Overview: You'll be responsible for developing,...
Maintenance Reliability Engineer
Job Summary:My client is seeking a Maintenance Reliability Engineer to enhance the reliability and performance of equipment and processes at our food and beverage manufacturing facility. This role will focus on implementing preventive and predictive maintenance strategies, analyzing equipment failures, and driving continuous improvement initiatives...